RESEARCH
FUNDED GRANTS

Dissemination
2022
The value of learning additive manufacturing technologies, starting from school years, has been widely recognized, but its implementation faces organizational and methodological challenges. The proposed project aims to develop, implement, and evaluate AM dissemination through the pathways of educating prospective and in-service teachers, high school and junior college students, and mechanical engineering students. Our team includes Technion researchers in digital technology education who are experienced teachers planning to conduct AM dissemination activities in their schools and colleges in the frame of the project. The common approach behind these dissemination activities will be based on the following principles:(1) using a cloud-based design platform Onshape allowing both in-class and remote education;(2) evaluation of student progress in 3D design and printing using the learning analytics software Education Enterprise; (3) fostering generic skills needed in the age of the Fourth Industrial Revolution. We hope that the learning activities that we will develop and conduct with the support of the Technion Additive Manufacturing Center will serve as pathways for further AM dissemination in school and higher education.
Additive Manufacturing Center works with different advanced applications like aerospace, automotive, biomedical, etc., which require use of various kinds of raw materials and involving different additive technologies, i.e., Electron Beam Melting (EBM), Selective Laser Sintering (SLS) and Binder Jetting Printing (BJP). Obviously, that a quality of as-built products, as well as their correspondence to existing standards, belong to a list of critical issues important for production of high-performance products with controlled mechanical, physical and surface properties. This dictates a necessity to study and implement the most advanced and effective NDT and failure analysis methods, considering standards requirements to as-built products. It is well-known, that one of the main advantages of Additive Manufacturing approach over the conventional one based on casting / bulk forming / machining, is a unique complex geometrical shape, which can be easily achieved in a combination with controlled material’s properties. Increasing demand in a geometrical complexity of the additively manufactured parts requires the most professional and effective use of the advanced software. A knowledge and a familiarity with modern existing software tools is a necessary condition to achieve a desired success in development and implementation of AM processing of high-performance parts. Fast developing advanced industries, like aerospace, automotive, defense and biomedical, is accompanied by increasing demand in ceramic parts with high geometrical shape’s complexity and dimensional stability. This is the reason for a growing interest in AM of ceramic and ceramic-matrix composite made parts. Therefore, scientific and technological dialog between Israeli applicative research-oriented centers, as well as AM producing companies, becomes important and is hoped to be fruitful and effective. Planned dissemination activities will include 3-days industrial workshop for Israeli industry, academy and start-ups.
2021
Metal Additive Manufacturing Center works with various key additive manufacturing applications including aerospace, automotive, industrial design, and biomedicine. One of the unique directions of the Center is development of new alloys, composites, and graded materials by additive manufacturing and AM-related processes.
Now there are two metal printing systems in our disposal: Direct Laser Metal Sintering (DMLS-process) by EOS and Electron Beam Melting by GE-Arcam. Those systems are successfully used for titanium, aluminum, and iron-based alloys.
Moreover, our Additive Manufacturing Center deals with design and topology optimization of complex aerospace components and patient-specific implants. Additional activities of the center are additive manufacturing courses and workshops for engineers that are performed in the frame of the Azrieli Continuing Education & Foreign Studies Unit, Technion –Israeli Institute of Technology. In these courses, the practice with modelling and machine/equipment operation is one of the crucial elements. Planned dissemination activities will include 3-days industrial workshop for Israeli industry, academy and start-ups.
We propose a new collaborative project course, between the Architecture and CS departments, where the goal of each team of students is to creatively apply geometric algorithms to fabricate objects using additive manufacturing and other computational fabrication methods. A pilot version of the course was given successfully in the Spring ‘21 semester, and we ask for funding for the next iteration of the course.
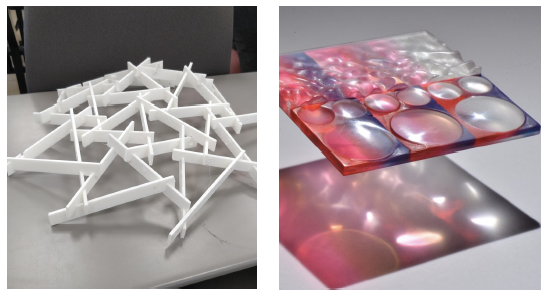
Equipment
2022
Advanced processes laboratory and Metal Additive Manufacturing Center work with various key additive manufacturing applications including aerospace, automotive, industrial design, and biomedicine. One of the unique directions of the Center is development of new alloys, composites, and graded materials by additive manufacturing and AM-related processes.
Now there are three printing systems in our disposal: ExOne M-Flex Binder Jetting, Direct Laser Metal Sintering (DMLS-process) by EOS and Electron Beam Melting by GE-Arcam. Those systems are successfully used for metals, ceramics and composites.
Moreover, our Additive Manufacturing Center deals with design and topology optimization of complex aerospace components and patient-specific implants.
Additional activities of the center are additive manufacturing courses and workshops for engineers that are performed in the frame of the Azrieli Continuing Education & Foreign Studies Unit, Technion –Israeli Institute of Technology. In these courses, the practice with modelling and machine/equipment operation is one of the crucial elements.
For the R&D needs, for educational benefits, and for design of new composite and functional graded materials our laboratory needs to perform hardware machine modification for finer powders, powder blends, and powders combination distribution. That equipment and proper installation will enable printing of denser parts; powder blends processing; and alternation of powders in one process with production of functional and functionally graded components.
3D bioprinting is an additive manufacturing process where biomaterials and living cells are combined to create engineered constructs that imitate natural living tissues. 3D bioprinting opens numerous possibilities for tissue engineering and regenerative medicine, disease modelling, drug discovery and food engineering. Extrusion and Digital Light Processing (DLP) are the most popular 3D bioprinting techniques. Extrusion offers multi-material printing from a vast palette of bioinks with various crosslinking mechanisms, while DLP based printing is capable of sophisticated geometric complexity, high resolution and enables very high manufacturing speed. The advantages of each technique make them perfectly complementary for many research areas. The Technion 3D-bioprinting center led by Prof. Shulamit Levenberg offers bioprinting services according to the user’s application. Currently, the center provides only extrusion-based bioprinting. We propose to upgrade and expand our facility by purchasing a BIONOVA X printer (Cellink), which is the most accurate DLP 3D bioprinter currently available, and the only model suitable for high-throughput multi-well DLP bioprinting. This will be the first printer of its kind at the Technion. The addition of this equipment to our infrastructure is expected to highly increase the use of the facility and strengthen the position of the Technion in the additive manufacturing field.
2021
3D metal and ceramic printing falls under additive manufacturing technologies, which saw significant advances in recent years. These technologies started to supplant classical subtractive based manufacturing methodologies and are gaining an increasing share of the manufacturing market. This is due to new, innovative possibilities to manufacture complex geometries and its relatively low price in comparison to more conventional manufacturing techniques. The particular prospects increase interest of different industries such as aerospace, automotive and medicine. There are various 3D printing technologies on the market which differ from each other by means of the original material supply and techniques to fuse metal layers into a complete model.
In order to expand the prototyping and research support capabilities of Technion a set of additive manufacturing tools for metals and ceramic materials to be acquired. In the scope of this infrastructure upgrade, a purchase of a special FDM printer (with a build volume of 180X230X200 [mm]) suitable for metal and ceramic filaments is requested along with two furnaces for debinding and sintering processes. Acquisition of this printer and the supporting equipment will supplement the existing metal and ceramic additive manufacturing machines in Technion and enable affordable additive manufacturing by introducing currently unavailable-in-house adapted FDM process.
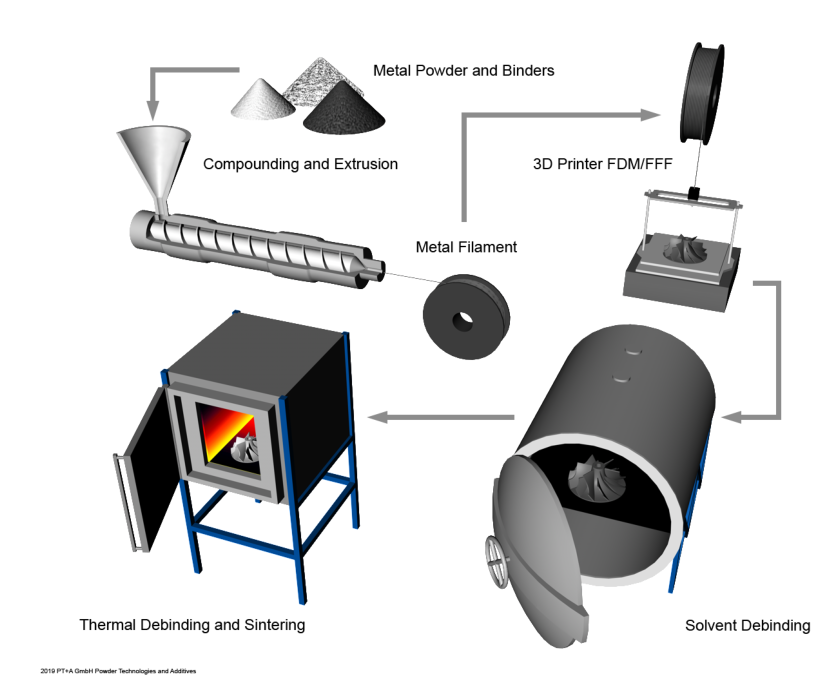
Maintenance
2022
The Stratasys J55 3D printer provides a unique combination of hardware and software, which allows for printing highly detailed and porous volumetric functionally graded materials. In this proposal, we request support for maintaining this printer for the benefit of research and teaching at the Technion.
One of the unique directions of the Metal Additive Manufacturing Center is the development of new alloys, composites, and graded materials by additive manufacturing and AM-related processes.
Now there are two metal printing systems at our disposal: Direct Laser Metal Sintering (DMLS-process) by EOS and Electron Beam Melting by GE-Arcam. The EOS M290 system is successfully used for titanium, aluminum, and iron-based alloys and soon we will start work with Inconel. Moreover, our Additive Manufacturing Center deals with the design and topology optimization of complex aerospace components and patient-specific implants.
Additional activities of the center are additive manufacturing courses and workshops for engineers that are performed in the frame of the Azrieli Continuing Education & Foreign Studies Unit, Technion –Israeli
Institute of Technology. In these courses, the practice with modeling and machine/equipment operation is
one of the crucial elements. For the R&D needs, for educational benefits, and for accurate prototyping for the industry we need to upgrade the software of EOS machine to stay on top of 3d printing progress. This step will significantly increase the capabilities of the machine.
2021
This proposal concerns the maintenance of a selective laser sintering (SLS) 3D printer, namely the Lisa Pro by Sinterit, which is capable of printing a variety of hard and soft polymeric materials. This additive manufacturing (AM) technique is advantageous over other AM techniques because the solid structures are sintered from a powder bed, thus allowing the fabrication of complex porous 3D lattices without requiring support structures for overhanging regions. Therefore, SLS enables the fabrication of lattice structures with internal pores that cannot be realized using other AM methods. Below we describe how we utilize these capabilities in our research on biomechanical interfaces. Nevertheless, the unique features of this 3D printer can serve a wide variety of researchers in different fields and for applications across the Technion faculties and research centers. External biomechanical devices such as prostheses, orthoses, and braces, are used by millions of people worldwide to recover from injury, restore mobility, reduce pain, etc. The mechanical interface between the device and the tissue region it interacts with must appropriately distribute the mechanical loads to fulfill its function. Successful biomechanical fit typically requires personalized custom devices, due to the large variability between patients. Today, the standard process for producing such custom devices involves plaster casting and a manual, labor-intense design and fabrication process, which is largely based on the technician’s experience. This trial-and-error process, which is insufficiently data-driven and lacks scientific rationale, often results in poorly fitted devices, which might cause pain and reduced mobility. Hence, our research group aims to develop novel methods for computationally designing data-driven patient-specific optimized biomechanical devices and to employ innovative AM techniques for fabricating enhanced designs which cannot be realized using other fabrication methods. Specifically, we employ lattice structures to locally vary the mechanical properties across the device interface with the body, by adjusting certain parameters of the lattice geometry. Fabrication of such structures is made possible by utilizing the SLS technology using various powdered materials.
Research
2022
Porous materials, such as foams, have numerous advantages in various applications. Closed-cell foams, in particular, exhibit excellent structural properties, especially in compression-dominant applications (e.g., cushioning and impact absorption), as well as unique thermal and acoustic insulation characteristics and low water absorption. Most existing additive manufacturing techniques enable only open-cell lattice structures to be printed, either because they require that the support material is removed from within the pores (e.g., in stereolithography), or they are limited by the overhang angles that can be supported (e.g., in fused deposition modeling). On the other hand, traditional closed-cell foam manufacturing techniques may be fast and efficient, but they lack the possibility to finely and locally control the foam properties and require the fabrication of molds to construct complex 3D shapes. Here, we propose a new additive manufacturing concept for fabricating engineered closed-cell foams, with locally variable pore size and distribution, which are unachievable using other techniques. The new concept involves the controlled deposition of gas bubbles encapsulated by a liquid material, which is then selectively solidified with the gas trapped inside. In the context of this project, we propose to develop a proof of concept by examining two different fabrication approaches and exploring a range of possible materials. Subsequently, we will select the most suitable approach and build a 3D printer, or modify an existing 3D printer, to work with the selected technique. Finally, we will manufacture various closed-cell engineered foam structures and analyze their mechanical properties. We hope that this new technique will open new possibilities for fabricating tailored functionally-graded closed-cell foams, for various applications.
Additive Manufacturing (AM) of metallic alloys is an emerging technology for producing complex geometries (e.g., porous structures, internal channels), which are either difficult or impossible to obtain using conventional metal forming techniques. Specifically, when applied to Shape Memory Alloys (SMA), AM can open the route for numerous new applications that cannot be implemented today in the fields of actuation, sensing, energy harvesting and heat management. Existing AM technologies for SMA are typically based on local melting of the metallic powder using a high energy beam. However, the repeated melting impairs the resulting microstructure, thus limiting the ability of the printed material to undergo a reversible thermo-elastic martensitic transformation. The latter is essential for shape-memory (SM) and super-elastic (SE) effects.
In this project we will study solid-state AM for Nickel-Titanium (Ni-Ti) system, which is the most common SMA. Solid-state AM implies that the metallic powder is not melted during the printing process, thus providing opportunities for controlling the microstructure and properties of the manufactured alloy by choosing the parameters of the raw material and the sintering and post-sintering treatments. In a previous research, our group studied AM of Ni-Ti using solid-state Lithography-based Metal Manufacturing (LMM). The manufactured samples displayed a reversible transformation and the ability to sustain very large stress values with negligible residual strains. However, the large volume fraction of organic additives in the starting powder mixture resulted in the formation of Ti-carbides during the sintering process, which limited the volume fraction that underwent the martensitic transformation.
In the current project, we will adopt a unique solid-state AM technology that is based on binder-jetting technology, developed exclusively by Tritone, Israel. In this process, the fraction of organic additives is much smaller than in LMM process. This is expected to significantly reduce the amount of impurities in the sintered Ni-Ti samples. Further, we will apply a pioneering approach for controlling the microstructure and properties of the AM material by controlling the grain size and microstructure of the raw-material powder. Microstructural and thermal characterization, followed by mechanical experiments will be conducted. Based on the experimental results, we will model the effects of powder microstructure, sintering and post sintering thermal treatments on the microstructure and on the SM and SE of AM Ni-Ti.
The project is expected to open the route for AM of SMA with good properties. Further, methods and knowledge gained by our pioneering approach for influencing the properties of the manufactured alloy by processing the raw material can be implemented in AM of other alloys. Based on the results of this seed project, which is the first collaboration of the PIs, we plan to propose an advanced R&D project to be submitted to the Israeli Innovation Authority.
Chronic wounds, mostly caused by complications of diabetes, have wide variability between patients in terms of shape, size, and vascular properties, thus calling for a personalized treatment. One emerging promising approach to treat chronic wounds is the use of skin grafts, which aim at mimicking skin extracellular matrix (ECM). To this end, the use of bioactive materials such as decellularized porcine skin ECM can lead to successful graft integration and promote regenerative processes. Moreover, through advanced wound imaging and additive manufacturing, these grafts can be personalized to perfectly fit each wound. As the skin regeneration is greatly affected by the oxygenation of the tissue, treatments for increasing oxygen concentration in and around the wound were suggested in combination with skin graft application. However, the lack of simple tools for measuring the actual oxygen concentration in and around the healing wound leads to poor monitoring of these treatments. The main goal of the proposed research is, therefore, to develop a personalized solution to actively treat chronic skin wounds and monitor the treatment progress through accurate sensing of wound oxygen levels. A personalized wound-specific artificial skin graft will be developed, and combined with personalized oxygen therapy, relying on wound-specific oxygen data. The geometry of real wounds will be determined by analysis of advanced 3D images and the grafts will be correspondingly tailored from porcine dermal ECM using additive manufacturing, thus harnessing the natural bioactivity of ECM in a controllable, tailor-made personalized graft. To monitor oxygen levels within the healing wound, the 3D skin graft will be incorporated during its manufacturing procedure with unique oxygen sensing paramagnetic micro-crystallites that will allow for real-time oxygen measurements, thus utilizing the skin graft not only as a temperate for tissue regeneration but also as a unique oxygen sensing platform. Altogether, this newly-developed unique theranostic approach will offer a complete personalized solution for chronic wound patients.
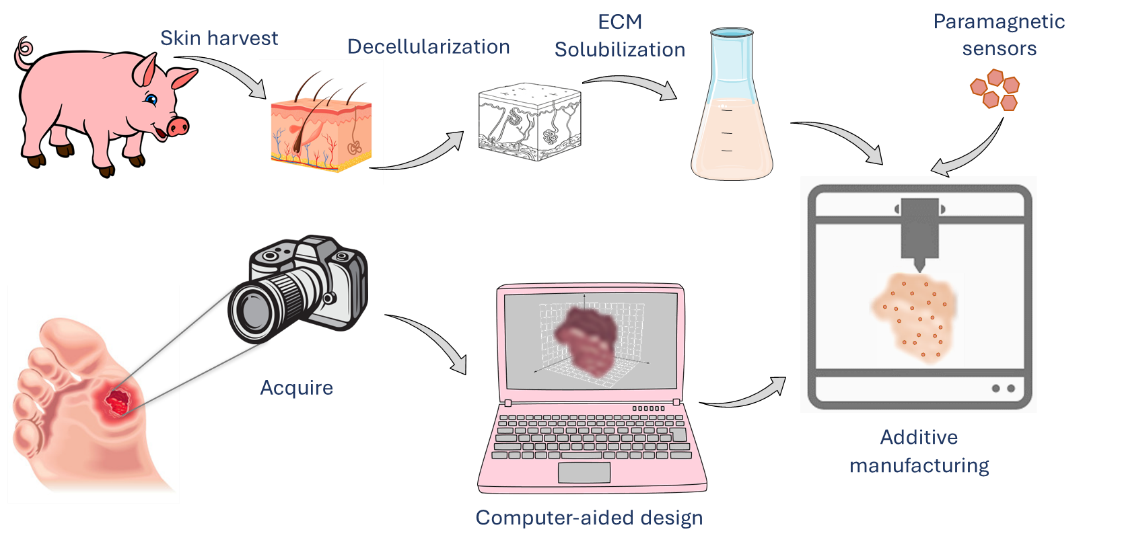
Cement and concrete production are responsible for nearly 6% of the world’s annual emissions of greenhouse gas carbon dioxide. Biodesign tries to address such challenges within architecture by integrating living materials as co-designers in fabrication processes. Development of such processes can potentially enhance ecological and environmental performance of construction materials by inheriting new properties such as degradability, recyclability, adaptation to growth, carbon dioxide fixation, air purification, and energy generation.
The current research proposes to develop an additive manufacturing (AM) protocol for material building blocks utilizing cyanobacteria as part of an interdisciplinary approach between microbiology and architecture. Unlike other bacteria, the significant ecological and financial advantage of using cyanobacteria in the process of cement manufacturing is their inherent ability to absorb and utilize CO2 from the atmosphere and induce calcium carbonate (CaCO3) precipitation as a result of their photosynthesis activity. Calcium carbonate is the main ingredient in limestone and cement and therefore can potentially substitute cement bricks with microbially bio-based cement that absorbs carbon dioxide gas and solidifies the bricks. In our proposal we aim to develop a CAD (computer-aided design) to CAM (computer aided manufacturing) workflow that provides the conditions that enable the living bacteria its functionality within an architectural fabrication process. Material ratios for cell viability and printability will be tested in relation to potential surface area exposure and optimised habitat geometry to develop an AM process capable of bridging between microbiological and architectural scales.
Based on preliminary results conducted jointly in the labs of Prof. Yechezkel Kashi and Asst. Prof. Shany Barath, inoculating colonies of cyanobacteria into solutions of sand and agar, our aim is to develop the basic technology of cyanobacteria building blocks as a novel architectural process. The specific research objectives are to; 1) develop a material fabrication protocol enabling the integration of cyanobacteria, sand and agar into cement bricks manufacturing process. 2) Utilize computational design tools and additive manufacturing workflows for laboratory prototyping 3) Developing assessment and provision of empirical guidelines into how the setting and environmental conditions as well as geometry influence colonization outcomes and solidification of building blocks. Developing such a process may improve the mutualism between building materials and their surroundings as it strives to foster new sustainable environments.
2021
Fabrication of optical components has not changed significantly in the past century and is based on mechanical grinding, machining and polishing that rely on complex and expensive infrastructure. Furthermore, such mechanical methods present challenges in fabrication of large or geometrically complex components. Modern manufacturing methods such as 3D printing, while capable of producing nearly arbitrary structures, cannot provide the required surface quality for optical applications.
We propose a theoretical and experimental study aimed at developing a novel methodology for the fabrication of optical components based on interfacial phenomena and polymer science. We term our approach ‘Fluidic Shaping’ to describe its core principle – the ability to take a volume of liquid, shape it into a desired form, and cure it to obtain a solid object. The method relies on negating gravitational forces that act on the liquid, which we achieve using buoyancy forces. By dictating the boundary conditions of the liquid, we vary the minimum energy state of the system, and drive the liquid interface into a desired shape. Within this project we will: (1) develop a theoretical model that would allow us to determine the range of optical components that could be produced using the method; (2) develop polymer materials that have the desired mechanical and optical properties for optical components; and (3) develop the first ‘LensMaker’ prototype – a stand-alone device capable of creating high quality optical components using the Fluidic Shaping method.
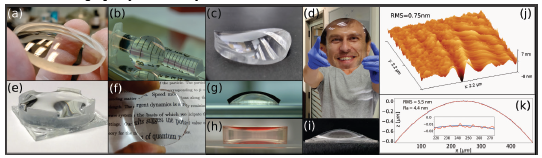
The proposed interdisciplinary research aims (i) to design and explore a novel method for the optimization of large-scale additive manufacturing methods of building elements made of cementitious materials; (ii) to develop and test innovative computational protocols for reducing waste material in the 3d printing process; (iii) to research and experiment with a customized, large-scale 8-axis robotic cell capable of distributing multiple types of aggregate-based composites. These objectives come as a response to the ever-increasing environmental stress due to the release of large quantities of waste material that result from conventional building modes and architectural design. We envision a construction protocol that combines knowledge in the computational design of optimized structures and novel methods of large-scale additive manufacturing specifically applied to cementitious materials. In light of the goals of TAMC, the proposed research will contribute as follows: (i) create and disseminate new knowledge in the field of large-scale aggregate-based AM; (ii) generate proof-of-concept prototypes to establish a benchmark that will be shared with the academic and professional communities; (iii) promote advanced digital fabrication methods in construction across the PI’s departments and curricula; (iv) train a new generation of high-quality personnel and scholars. The proposed research stems from preliminary investigations performed at the PI’s laboratories, and recently published in peer-reviewed academic journals and presented at high-profile conferences.
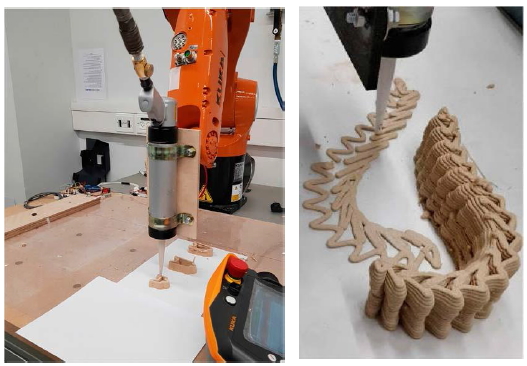
Catheters are among the most frequently used medical tools in modern therapies. Several diseases are treated by catheters (e.g. hydrocephalus) in cardiovascular, urological, gastrointestinal neurovascular, and ophthalmic diseases. In fact, approximately 150 million intravascular catheters are implanted annually in the United States alone. However, although very efficient, following their insertion, catheters are subjected to numerous complications including resistance to flow, blockage and mechanical malfunctions and being subjected to host-immune response and microbial infection. To overcome these complications, we propose to implement three-dimensional (3D) printing technology in order to develop next generation of catheters with improved functionality and liquids flowability. Our suggested technology is based on imaging data on final destiny site (via CT or MRI) in such a way that it fit the need in the body in a personalized manner. Moreover, we present a first of its kind development composed of smart polymeric coating with proper surface chemistry that can respond in dynamic way to the 3 main catheters challenges: inflammation, fibrosis and infection via chemical intramolecular rearrangement in the functional moieties of the coating. The functional moieties will be designed to rapidly respond to minimal changes in catheter’s nearby physiological microenvironment, thus boosting treatments successfulness. In this study we example the unmet medical needs referencing hydrocephalus as disease model, which we highly believe 3D printing may offer unique solution with boarder implication to the wider medical implants and vascular grafts field.
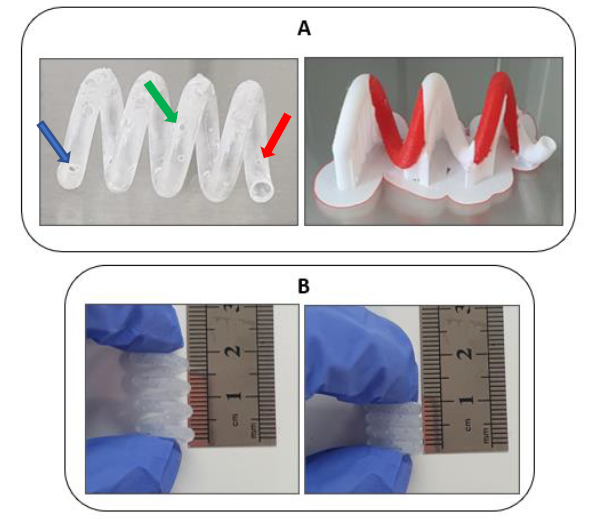