RESEARCH
COMPLETED

Dissemination
2021
The value of learning additive manufacturing technologies, starting from school years, has been widely recognized, but its implementation faces organizational and methodological challenges. The proposed project aims to develop, implement, and evaluate pathways of AM dissemination to high school students majoring in technology and engineering education, as well as prospective and in-service STEM teachers. Our team includes researchers in digital technology education, Ph.D. students who are experienced teachers leading AM dissemination for different categories of learners and doing research on the subject. Our team will teach modules on design and 3D printing in STEM teacher education courses, conduct outreach programs and workshops for school students, and teacher professional development courses in the subject. We hope that the learning activities that we will develop and conduct with support of TAMC will serve as models for further AM dissemination to the school system.
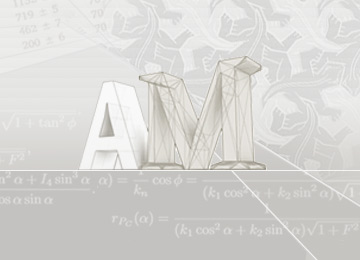
Equipment
2021
Materials produced by organisms, in contrast to synthetic materials, must be formed under ambient conditions and from a limited selection of elements. Nevertheless, living organisms demonstrate elegant strategies for creating 3D materials with specific functions. We recently identified a remarkable biostrategy for growing 3D calcite optical lenses found in the brittle star Ophiocoma wendtii via supersaturated amorphous precursors.
The organism first deposits a supersaturated amorphous precursor of Mg-calcium carbonate in the desired 3D structure which only afterwards undergoes crystallization an ambient condition. This allows not only for the creation of complex 3D structures and morphologies but also allows the formation of metastable Mg-rich nanoprecipitates and layers of varying chemical composition which toughen the otherwise brittle structure.
Based on this discovery, we now propose translating this strategy into a novel synthetic route for advanced 3D fabrication of materials (two patents have been submitted). We aim to develop and utilize supersaturated amorphous precursor powders as the starting material for 3D printing followed by on-demand low-temperature crystallization of the 3D-printed objects. Moreover, by controlling the composition of these precursors we will form 3D objects that contain designed spatial compositional inhomogeneities. We also aim to understand the correlation between the micro- and nanorostructure and the mechanical properties of the newly developed 3D printed functional materials.
We have shown preliminary results which strengthen the feasibility of utilizing an amorphous material in robocasting additive manufacturing and now want to move forward and expand this research with SLS-based 3D printing. The latter can enable the printing of a wide range of materials including ceramics, composites and metals. Despite the growing number of 3D printers available on campus of the Technion, such an SLS printer is as yet lacking and is of great interest to many research groups both on campus as well as from industry.
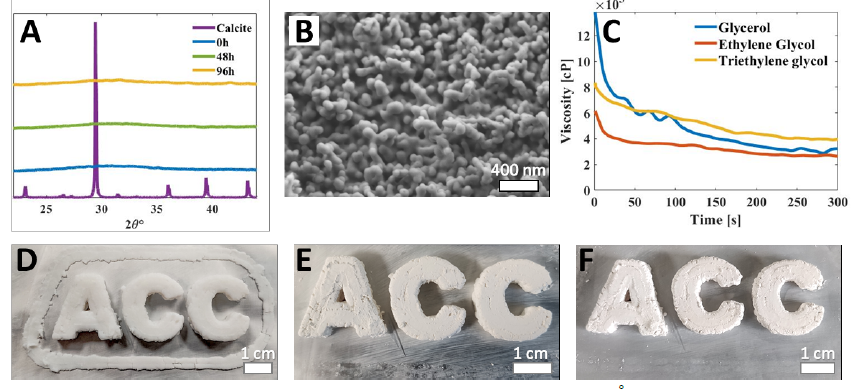
The Aeroelasticity Laboratory at the Aerospace Engineering faculty is dedicated to computational and experimental research of aero-structural interactions. Our current focus is on very flexible structures, shape sensing and control via optical fibers, utter prediction and mitigation, and more. We have gained significant experience with 3D printed wing models for aeroelastic testing. This culminated in a 3-years undergraduate students capstone project, hosted in the Aeroelasticity Laboratory, designing, building, and flying an all 3D printed UAV for aeroelastic research and technology demonstration.
The equipment required in the TAMC proposal includes a Polymer printer and structural excitation and measurement accessories. An in-house printer would be a tremendous support for the high volume printing needed in the lab monthly. The test equipment is required to supplement the lab’s existing testing capabilities for material properties tests, loading tests, and ground vibration tests. Such tests are essential to any load-carrying 3D printed design and will be offered by the Aeroelasticity Laboratory to the TAMC community.
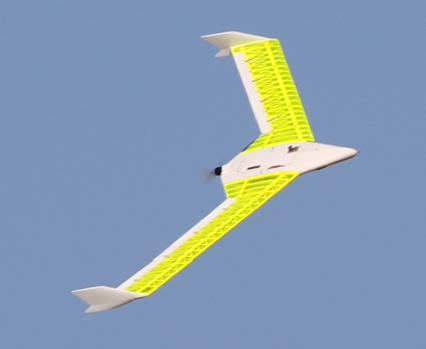
Maintenance
2021
Metal Additive Manufacturing Center works with various key additive manufacturing applications including aerospace, automotive, industrial design, and biomedicine. Moreover, one of the unique directions of the Center is development of new alloys, composites, and graded materials by additive manufacturing and AM-related processes.
Now there are two metal printing systems in our disposal: Direct Laser Metal Sintering (DMLS-process) by EOS and Electron Beam Melting by GE-Arcam. These systems utilize full melting of the powder with production of fully dense metal parts. Those systems are successfully used for titanium, aluminum, and iron-based alloys.
In the near future, we plan to install another metal printing system – Markforged Metal X. This AM process combines metal injection molding (MIM) and fused deposition modelling (FDM). Metal X enables producing parts from stainless steel, Inconel, copper, etc. Moreover, the machine itself and the used materials (filaments) are much cheaper than Powder Bed Fusion (PBF) systems. Metal X made parts require post-treatment: “washing” off the polymer and densifying heat treatment (sintering). All these production steps need to be prepared by careful organization of the working space for printing machine, washer, and sintering furnace. This equipment requires connecting of electricity, argon, air, water, and compliance with fire safety and ventilation.
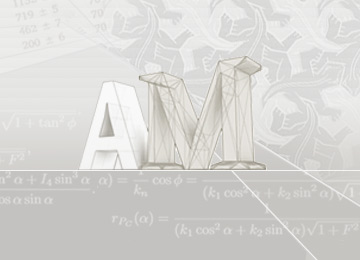